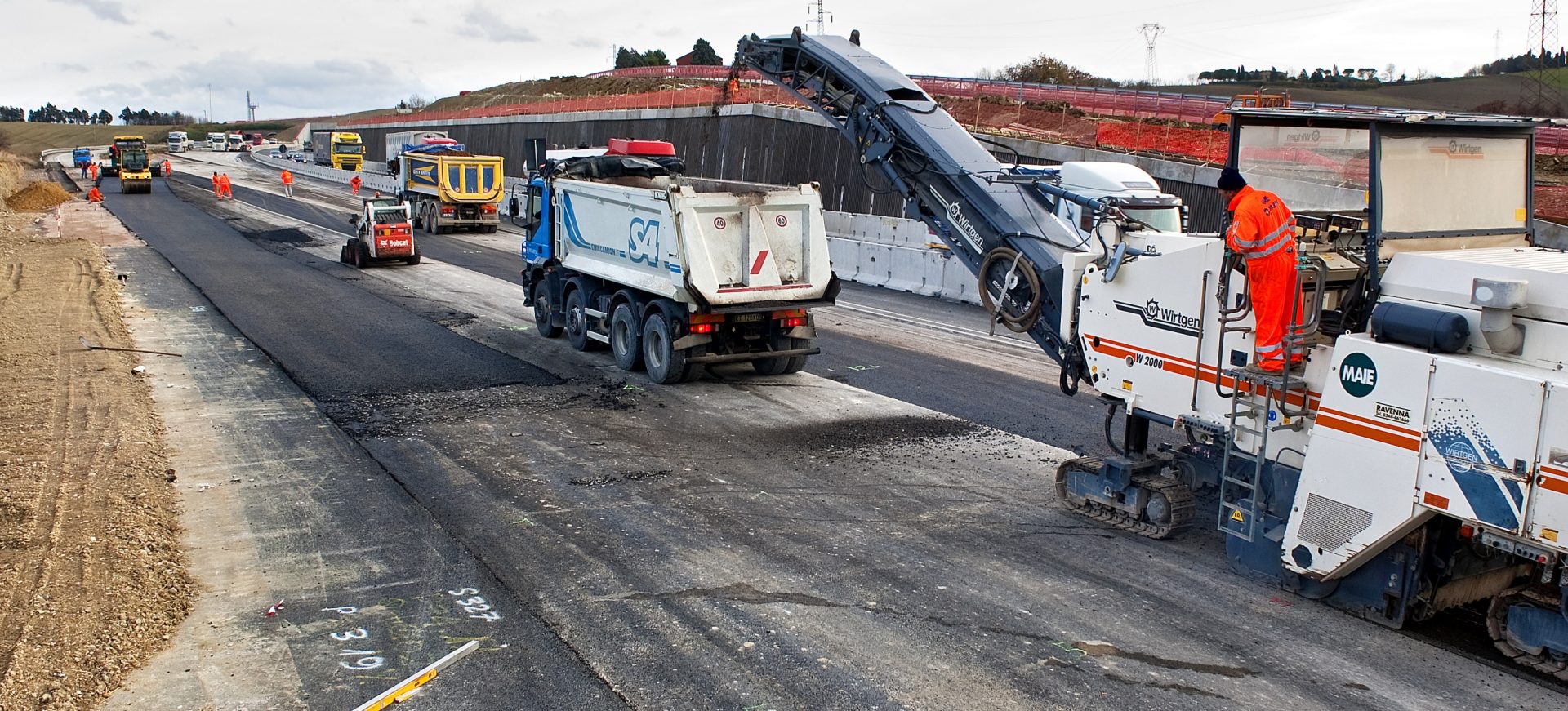
Extension works of the 3rd lane from North Rimini to Pedaso
Concerning the Bologna – Bari – Taranto motorway.
Located in the Cattolica – Fano section. Lot 2 from Km 145 + 537 to Km 173 + 702
Description of the intervention
With reference to the extension works of the 3rd lane from North Rimini to Pedaso on the Bologna – Bari – Taranto motorway, located in the Cattolica – Fano stretch. Lot 2 from Km 145 + 537 to Km 173 + 702, in November of 2011, following a private negotiation, the “PENTAPOLI” Società Consortile a r.l. has entrusted Pesaresi Giuseppe S.p.A. with the supply and installation of bituminous conglomerates type Base 0/30 mod. hard and Binder 0/18 mod. hard.
The construction of the pavement in bituminous conglomerate on the stretches in extension of the motorway, took place on embankments – laying surfaces in mixed cement prepared by the Customer.
After topographical positioning of the road sections to trace the plano-altimetric dimensions of the new platform, before the laying of the bituminous conglomerate or at the same time as the laying of the first base layer, our workers proceeded to install longitudinal guide wires positioned at the height of the binder, so as to create for the operator in charge of guiding-adjusting the paver, both a longitudinal and transversal dimension and direction reference, able to determine thanks to it, the thickness of the intermediate strips necessary to cover the the entire width of the new platform, which in cases of fully asymmetrical expansion reached up to about 15.00 meters.
The road package for the project bituminous conglomerate, provided for a 0/30 base layer with hard modified bitumen of the total thickness, measured after rolling, of 25 cm, carried out by laying a first layer of the finished thickness of about 15 cm and a second layer of about 10 cm, taking care to offset the longitudinal joints by varying the width of the single strips. The spreading took place in layers in order to guarantee the correct compaction of the conglomerate and to guarantee the achievement of the percentage of voids declared in the prequalifications. For this purpose, the rolling of the conglomerate takes place through the simultaneous use of a static rubber roller brand Bomag BW27RH weighing 24 tons. and a vibrating iron roller brand Bomag BW174AD weighing 10 tons.
Before the execution of the second base layer, and of the binder, the attack coat was made by spreading acidic bituminous emulsion, then proceeding to trace the exact thicknesses missing to reach the expected thickness, identifiable by using transverse wires referring to the traced sections.
The laying of the binder took place by means of a single layer of the minimum projected thickness of 5 cm, longitudinally following the yard tracing threads, and transversely the dimensions further traced on the last base layer, between the individual strips, in order to correct any slight depressions and / or imperfections on the underlying layer, always paying maximum attention to the offset of the longitudinal joints. During the laying of the binder, the containment edge in bituminous conglomerate was created, where necessary, about 10 cm wide and about 15 cm high.
By means of padding, the existing road section was raised and re-profiled. These were organized by the client in several phases compatible with the progress of the work, in day and / or night work shifts. In the case of temporary paddings subject to opening to vehicular traffic, or in any case each time conglomerate floors made at different times are joined, the previous paving has been scarified in order to revive, clean and homogenise the point of attachment between the new and old bituminous conglomerate.
Subsequently, in February 2012, the Client “Pentapoli S.C.a R.L.”, extended the contract entrusted to us to the construction works of the pervious wear layer. The intervention was carried out in several stages:
- 1st section, from Cattolica (Km 145 + 537 at the beginning of the lot) to Pesaro (Km 163 + 000, around Case Bruciate), north and south carriageway,
- 2nd section, from Fano (Km 173 + 702 at the end of the lot) to Pesaro (Km 163 + 000 approximately), south and north carriageway.
Before laying the pervious pavement type, 3D milling was carried out to optimise the levels of the current state. The purpose is to level the laying surface of the pervious wear by scarifying the upper parts, or rather refilling the depressed areas with bituminous conglomerate. In this way, an optimisation of the project level is obtained and a leveling of the slight imperfections inevitably present on the binder plane, due to the execution of the same in several fragmented phases.
The surface thus obtained was perfectly cleaned with the aid of a sweeper, to be sprinkled first with a modified attack coat and then with filler, in order to prevent traction to the tire laying surface of the vehicles used for the transport and laying of the conglomerate.
The laying of the pervious wear pavement took place by means of a rubber-coated vibratory finishing machine, equipped with a 12 m Big Multiplex system with three laser sensors. The formation of the wear layer, on the previously leveled surface, took place by spreading at a constant thickness of 4 cm (rendered after rolling), with the aid of the altimetric control plan tracking, useful to correct further and any flatness defects still present.
Compatibly with the construction sites, the paving was organised over one or more work shifts so as to ensure longer stripes without recovery points and avoid foreseeable stops, which would have resulted in an inevitable cooling of the conglomerate. Where possible, two paver-side pavers were used at the same time, thus creating the “hot” joint of the two strips. For the longitudinal jointing of pavements carried out at different times, the attachment tooth has always been milled, so as to revive and regularise the same, while eliminating the most marginal part of the previous pavement.
Below, the most characteristic elements of the tender in question are reported by points:
Intervention specification
CONTRACTING AUTHORITY.
Company “AUTOSTRADE PER L’ITALIA S.p.A.”
CUSTOMER:
Temporary grouping of companies “PENTAPOLI” S.c.a.r.l.
AUCTION CRITERION OF WORKS:
Work in subcontracting
AMOUNT OF CONTRACT:
€ 23.840.000,00
WORK CATEGORIES:
OG3 € 23.840.000,00
START DATE AND FINISH DATE OF WORKS:
December 2011 – July 2014