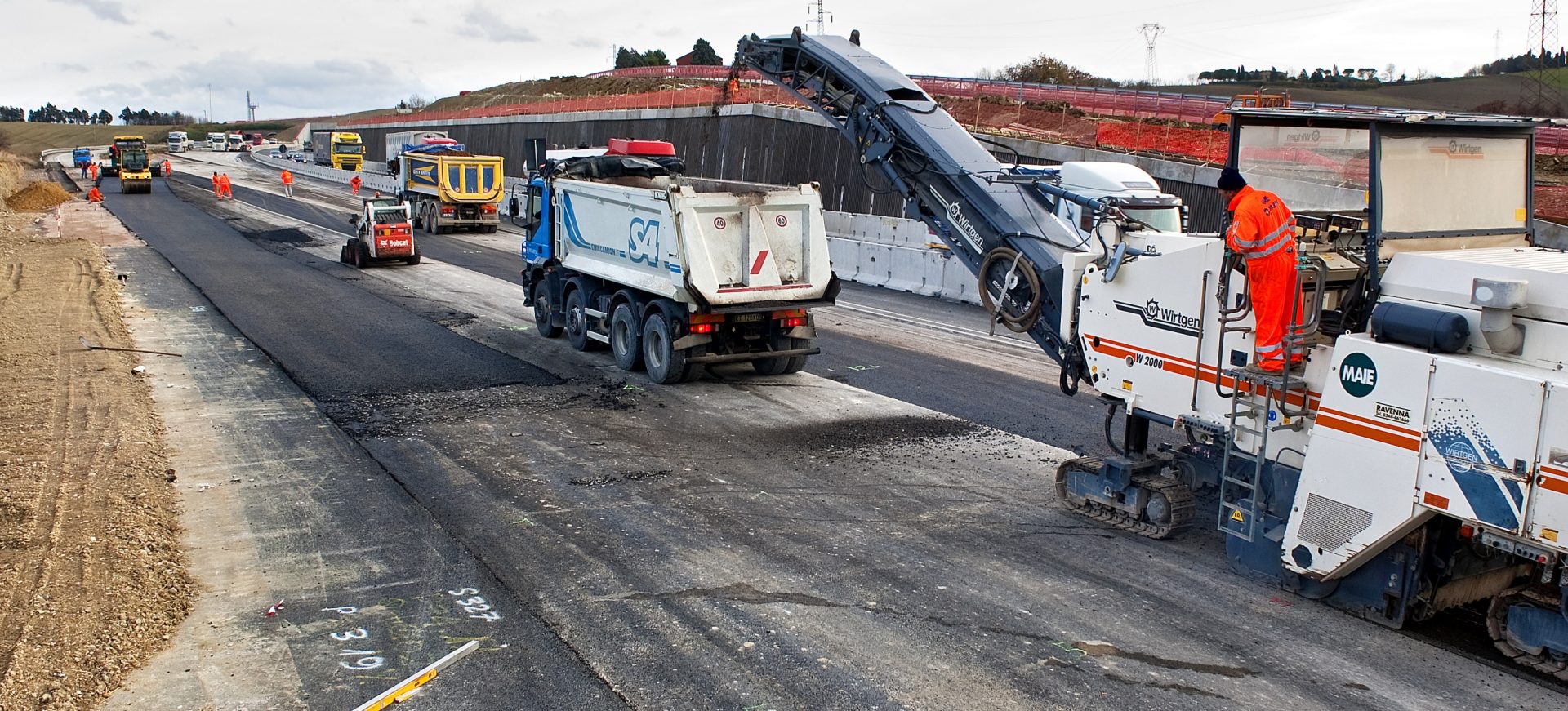
Lavori di ampliamento alla 3^ corsia da Rimini nord a Pedaso
ricadenti nell’autostrada Bologna – Bari – Taranto, ubicati nel tratto Cattolica – Fano.
Lotto 2 dal Km 145+537 al Km 173+702 – Codice appalto n° 0368/A14.
Realizzazione di pavimentazione stradale in conglomerato bituminoso tipo base 0/30 modificata hard, binder 0/18 modificato hard, e tappeto d’usura drenante – ipodrenante.
Descrizione dell’intervento
Con riferimento ai Lavori di ampliamento alla 3^ corsia da Rimini nord a Pedaso ricadenti nell’autostrada Bologna – Bari – Taranto, ubicati nel tratto Cattolica – Fano. Lotto 2 dal Km 145+537 al Km 173+702, nel mese di novembre del 2011, a seguito di trattativa privata, la “PENTAPOLI” Società Consortile a r.l. ha affidato alla Pesaresi Giuseppe S.p.A., la fornitura e posa dei conglomerati bituminosi tipo Base 0/30 mod. hard e Binder 0/18 mod. hard.
La realizzazione della pavimentazione in conglomerato bituminoso sui tratti in ampliamento della sede autostradale, è avvenuta su rilevati – piani di posa in misto cementato predisposti dal Committente.
Previo posizionamento topografico delle sezioni stradali a tracciamento dell’ingombro plano-altimetrico della nuova piattaforma, prima dell’esecuzione delle stese del conglomerato bituminoso o contestualmente alla posa del primo strato di base, le nostre maestranze hanno proceduto all’installazione di fili guida longitudinali posizionati alla quota del binder, in modo da creare all’operatore addetto alla guida-regolazione della vibrofinitrice, un riferimento di quota e direzione, sia longitudinale, sia trasversale, in grado di determinare grazie ad esso, lo spessore delle strisciate intermedie necessarie a coprire l’intera larghezza della nuova piattaforma, che nei casi di ampliamento interamente asimmetrico arrivava fino a circa 15.00 metri. Il pacchetto stradale per il conglomerato bituminoso di progetto, prevedeva uno strato di base 0/30 con bitume modificato hard dello spessore totale, misurato dopo la rullatura, di cm 25, eseguito mediante la stesa di un primo strato dello spessore finito di cm 15 circa e una seconda stesa di cm 10 circa, avendo cura di sfalsare le giunte longitudinali variando la larghezza delle singole strisciate. La stesa è avvenuta per strati al fine di garantire il corretto costipamento del conglomerato e garantire il raggiungimento delle percentuali di vuoti dichiarati nelle prequalifiche. A tal fine la rullatura del conglomerato avviene mediante l’utilizzo simultaneo di un rullo gommato statico marca Bomag BW27RH del peso di 24 Ton. e un rullo in ferro vibrante marca Bomag BW174AD del peso di 10 Ton.
Prima dell’esecuzione del secondo strato di base, e del binder, è stata realizzata la mano d’attacco mediante lo spargimento di emulsione bituminosa acida, procedendo poi al tracciamento degli spessori esatti mancanti al raggiungimento dello spessore previsto, individuabili mediante l’utilizzo di fili trasversali riferiti alle sezioni tracciate.
La stesa del binder è avvenuta mediante uno strato unico dello spessore minimo previsto di progetto di cm 5, seguendo longitudinalmente i fili di tracciamento di cantiere, e trasversalmente le quote ulteriormente tracciate sull’ultimo strato di base, tra le singole strisciate, in modo di correggere eventuali lievi avvallamenti e/o imperfezioni presenti sullo strato sottostante, ponendo sempre la massima attenzione allo sfalsamento delle giunte longitudinali. Durante la stesa del binder è stato realizzato, ove necessario, il bordino di contenimento in conglomerato bituminoso, largo circa cm 10 e alto circa cm 15.
Mediante imbottiture si è provveduto all’innalzamento in quota e riprofilatura della sezione stradale esistente. Queste sono state organizzate dalla committenza in più fasi compatibili con l’avanzamento dei lavori, in turni di lavoro diurni e/o notturni. Nel caso di imbottiture provvisorie soggette ad apertura al traffico veicolare, o comunque ogni volta che vengono giuntate pavimentazioni in conglomerato realizzate in tempi diversi, è stata prevista la scarifica della stesa precedente al fine di ravvivare, pulire e rendere omogeneo il punto di attacco tra il nuovo ed il vecchio conglomerato bituminoso.
Successivamente, nel mese di febbraio del 2012, la Committente “Pentapoli S.C.a R.L.”, ha esteso la commessa a noi affidata ai lavori di realizzazione del manto di usura drenante. L’intervento è stato attuato in più fasi:
- 1° tratto, da Cattolica (Km 145+537 inizio lotto) a Pesaro (Km 163+000 circa località Case Bruciate), carreggiata Nord e Sud,
- 2° tratto, da Fano (Km 173+702 fine lotto) a Pesaro (Km 163+000 circa), carreggiata sud e nord.
Prima della stesa del tappeto d’usura di tipo drenante, si è proceduto mediante fresatura 3D all’ottimizzazione delle livellette dello stato di fatto. Lo scopo è quello di livellare il piano di posa dell’usura drenante mediante scarifica delle parti alte, ovvero ricarica con conglomerato bituminoso delle aree depresse. In questo modo si ottiene un’ottimizzazione della livelletta di progetto ed un livellamento delle lievi imperfezioni inevitabilmente presenti sul piano del binder, dovute all’esecuzione dello stesso in più fasi frammentate.
La superficie così ottenuta è stata perfettamente pulita con l’ausilio di una motospazzatrice, per essere cosparsa dapprima con una mano d’attacco modificata e successivamente con filler, allo scopo di impedire l’adesione con la superficie di posa dei pneumatici dei mezzi adibiti al trasporto e alla stesa del conglomerato.
La stesa del tappeto d’usura drenante è avvenuto mediante macchina vibrofinifinitrice gommata, dotata di sistema Big Multiplex da 12 mt con tre sensori laser. La formazione dello strato di usura, sulla superficie precedentemente livellata, è avvenuta mediante stesa a spessore costante di cm 4 (resi dopo la rullatura), con l’ausilio del tracciamento plano altimetrico di controllo, utile a correggere ulteriori ed eventuali difetti di planarità ancora presenti.
Compatibilmente con le aree cantierizzate, la stesa è stata organizzata su uno o più turni di lavoro così da garantire strisciate più lunghe prive di punti di ripresa ed evitare soste prevedibili, che avrebbero comportato un’inevitabile raffreddamento del conglomerato. Ove possibile, si è provveduto all’impiego contemporaneo di due vibrofinitrici affiancate, realizzando così la giunzione “a caldo” delle due strisciate. Per la giunzione longitudinale di stese eseguite in tempi diversi, si è sempre provveduto alla fresatura del dente di attacco, così da ravvivare e regolarizzare lo stesso, eliminando al contempo la parte più marginale della precedente stesa.
A seguire, si riportano per punti gli elementi più caratterizzanti dell’appalto in oggetto:
Specifiche intervento
STAZIONE APPALTANTE:
Società “AUTOSTRADE PER L’ITALIA S.p.A.”
COMMITTENTE:
Raggruppamento temporaneo di imprese “PENTAPOLI” Soc. Consortile a r.l.
CRITERIO DI AGGIUDICAZIONED DEI LAVORI:
Lavoro in Subappalto
IMPORTO DI CONTRATTO:
€ 23.840.000,00
CATEGORIE D’OPERA:
OG3 € 23.840.000,00
DATA DI INZIO E FINE LAVORI:
dicembre 2011 – luglio 2014